The automotive industry continually evolves, driving advancements in every component used in vehicle manufacturing. Among these components, the humble automotive door seal rubber plays a pivotal role in ensuring a seamless driving experience, offering not just comfort but also safety and durability.
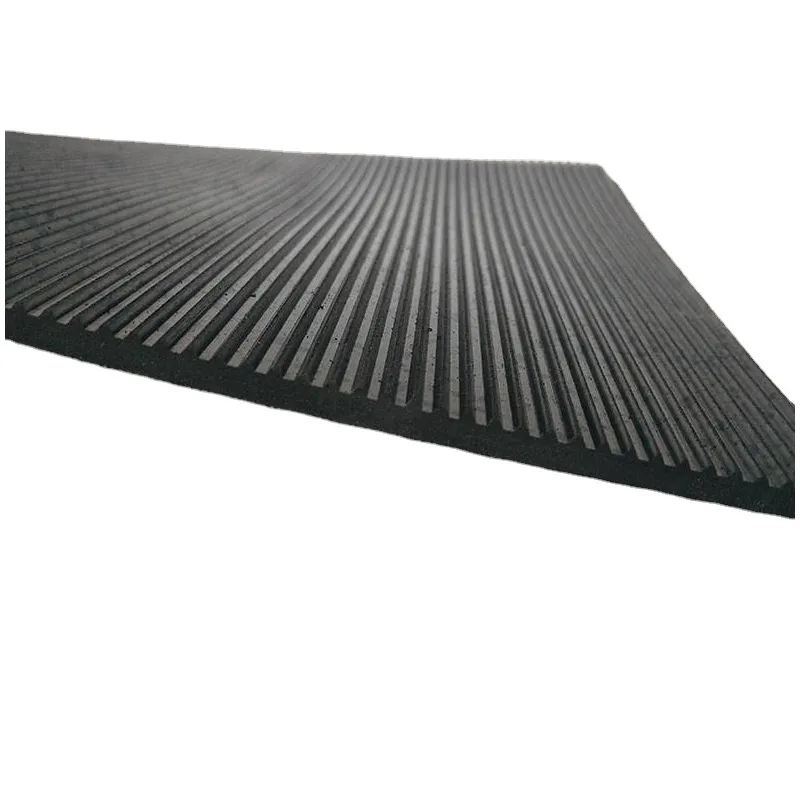
At first glance, the door seal rubber might seem like a trivial part of a vehicle, yet this component is engineered with precision and expertise to fulfil various critical functions. As a true buffer between the interior cabin and the external environment, door seal rubbers help in noise reduction, temperature control, and preventing water and dust ingress.
Professionals in the automotive industry understand that door seals are tailored to meet specific requirements of vehicle models, making use of various materials such as EPDM (Ethylene Propylene Diene Monomer). This synthetic rubber is celebrated for its remarkable resistance to weather, ozone, and ultraviolet rays, boasting longevity even under tough environmental conditions. EPDM rubber used in door seals enables the durability that vehicles demand, offering resilience that withstands both scorching summers and freezing winters.
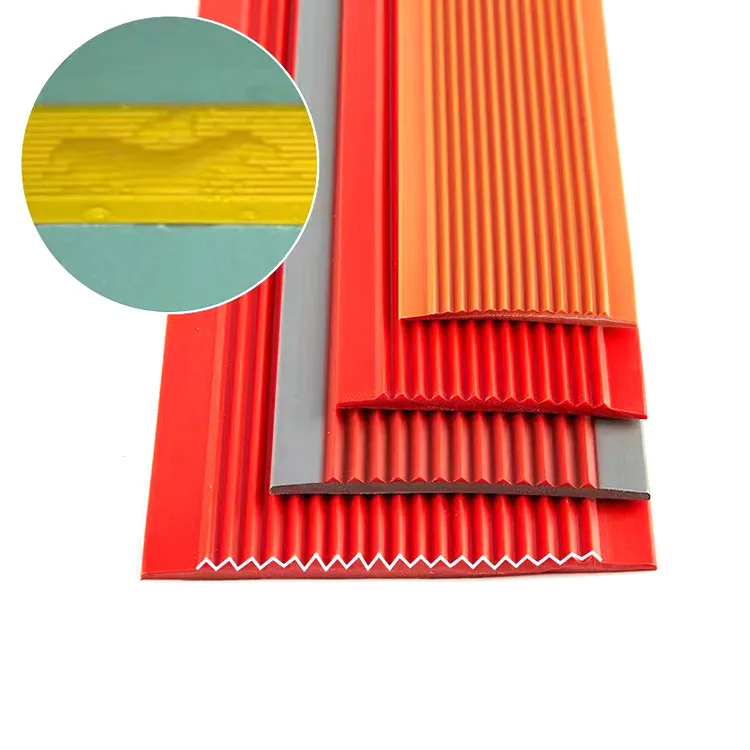
During the vehicle manufacturing process, selecting the right door seal entails more than just considering material durability. The engineering team meticulously analyzes the seal's compression force deflection and the appropriate cross-sectional design for optimal sealing performance. This comprehensive approach ensures that the seal maintains its elasticity and shape over time, irrespective of the number of times the door is opened and closed.
Longevity and performance of door seal rubbers also enhance with advanced co-extrusion techniques. By blending different materials, manufacturers can achieve combinations of flexibility and toughness along the length of the seal. This specialized manufacturing technique underlines the level of expertise required to produce efficient door seals, ensuring they meet vehicle safety standards while ensuring passenger comfort.
automotive door seal rubber
Expertise in manufacturing isn't limited to the production process but extends to product design. Manufacturers leverage computer-aided design (CAD) and finite element analysis (FEA) to predict how door seals will behave under various conditions. Through simulations, engineers assess the impact of temperature fluctuations, pressure differentials, and material fatigue. These predictive analyses contribute significantly to a product's reliability, giving automakers confidence in the components they integrate into vehicles.
Authoritativeness within this domain isn't confined to production capabilities but is also reflected in quality assurance and testing. Before ever reaching consumers, door seal rubber products undergo rigorous testing—simulating thousands of cycles of door opening and closing, exposure to extreme temperatures, and subjection to chemical and environmental elements. These tests certify that the seals comply with stringent automotive industry standards, such as the ISO/TS 16949, dedicated to upholding quality in automotive production.
Not to be overlooked is the critical aspect of trustworthiness that hinges on a manufacturer's commitment to sustainability. In an era where eco-friendliness and sustainability are becoming non-negotiable, manufacturers are redefining their production processes to minimize environmental impact. Utilizing recyclable materials and improving the energy efficiency of production facilities are becoming standard practices. This commitment not only enhances the brand's reputation but also aligns with global efforts to promote eco-conscious manufacturing.
From conception to production, and finally, to its role in the finished vehicle, the journey of automotive door seal rubber underscores the convergence of experience, expertise, authoritativeness, and trustworthiness. It's a narrative woven by multiple stakeholders, including material scientists, engineers, designers, quality assurance professionals, and sustainability experts—all working in tandem to ensure that what may seem like a simple component significantly elevates a vehicle's performance and consumer satisfaction.
As vehicles evolve to meet more demanding consumer standards and regulatory requirements, the need for superior-quality automotive door seals will become increasingly imperative. Future innovations may harness advanced materials such as graphene composites or intelligent sealing systems that adapt to environmental conditions, pushing the boundaries of what door seal rubbers can achieve. The continuous advancements in this field underline the ongoing commitment to enhancing vehicle integrity, reinforcing the importance of automotive door seal rubber as an integral component of modern automobiles.